Dry rolling granulator, also known as dry powder granulator, is commonly used for the molding and pressing of dry powder raw materials. It is also known as organic fertilizer when it is used for the pressing of powdered organic fertilizer. Dry rolling granulator adopts dry rolling technology to make dry powder materials with water content ≤ 10% into granular products by external pressure.
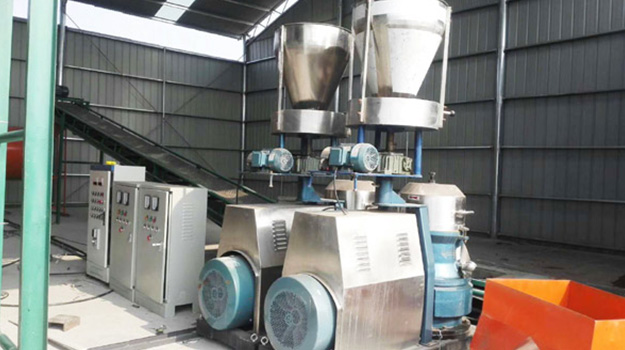
All kinds of dry powder materials are feeded from the feeding port of the equipment, and enter the counter roll through degassing and spiral pre loading. Under the extrusion pressure of the counter roll, the materials are plastically deformed and compressed into flakes. The flake materials are crushed, granulated, screened and other processes to obtain granular products.
The extrusion force can be adjusted by the pressure of the hydraulic cylinder according to the needs of granulation
Working principle of dry rolling granulator
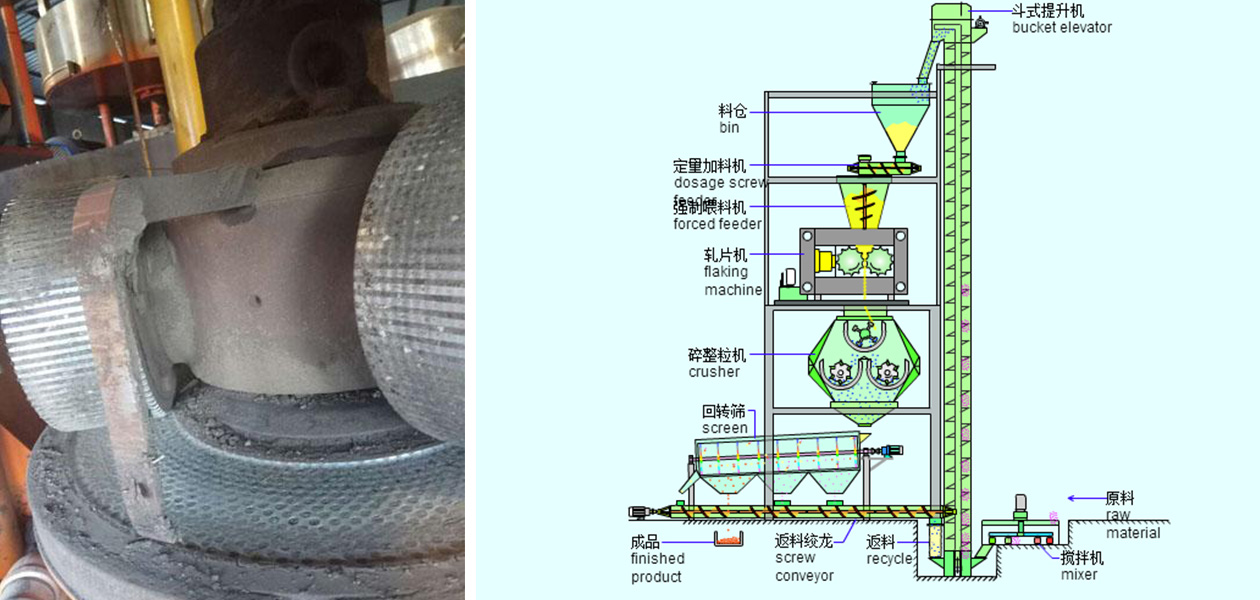
The organic fertilizer dry rolling granulator is driven by a motor, and the belt and pulley are transmitted to the driving shaft through the reducer. It works in the opposite direction by synchronizing with the driven shaft through the split gear. All kinds of dry powder materials are added from the hopper at the top of the equipment, and enter two equal rollers through degassing and spiral preloading. The rollers rotate relatively, and the materials are forcibly sent between the two rollers. The rollers bite the materials into the roll gap for forced compression. After the materials pass through the compression area, the surface tension and gravity of the materials make them naturally come out.
It is extruded by rollers, demoulded and made into balls, and then transmitted to the crushing Screen Studio through a pair of chains. The finished products (balls) are sieved and separated, and then the returned materials are mixed with the new materials, and then granulated. With the continuous rotation of the motor and the continuous entry of materials, batch production can be achieved.
The stripped finger shaped lumps enter the granulator and are broken by the rotating knife row. The crushed materials enter the granulator, and the granulars and some powdered materials enter the rotary vibrating screen for screening through the rolling knife row.
Qualified products are sent to the finished product warehouse through the conveyor.
The material under the powder screen is sent back to the raw material bin for secondary rolling through the conveyor. The extrusion pressure can be adjusted by the hydraulic system according to the needs of granulation operation.
By changing the grooving form of the roll surface, sheet, strip, flat ball and other materials can be obtained.